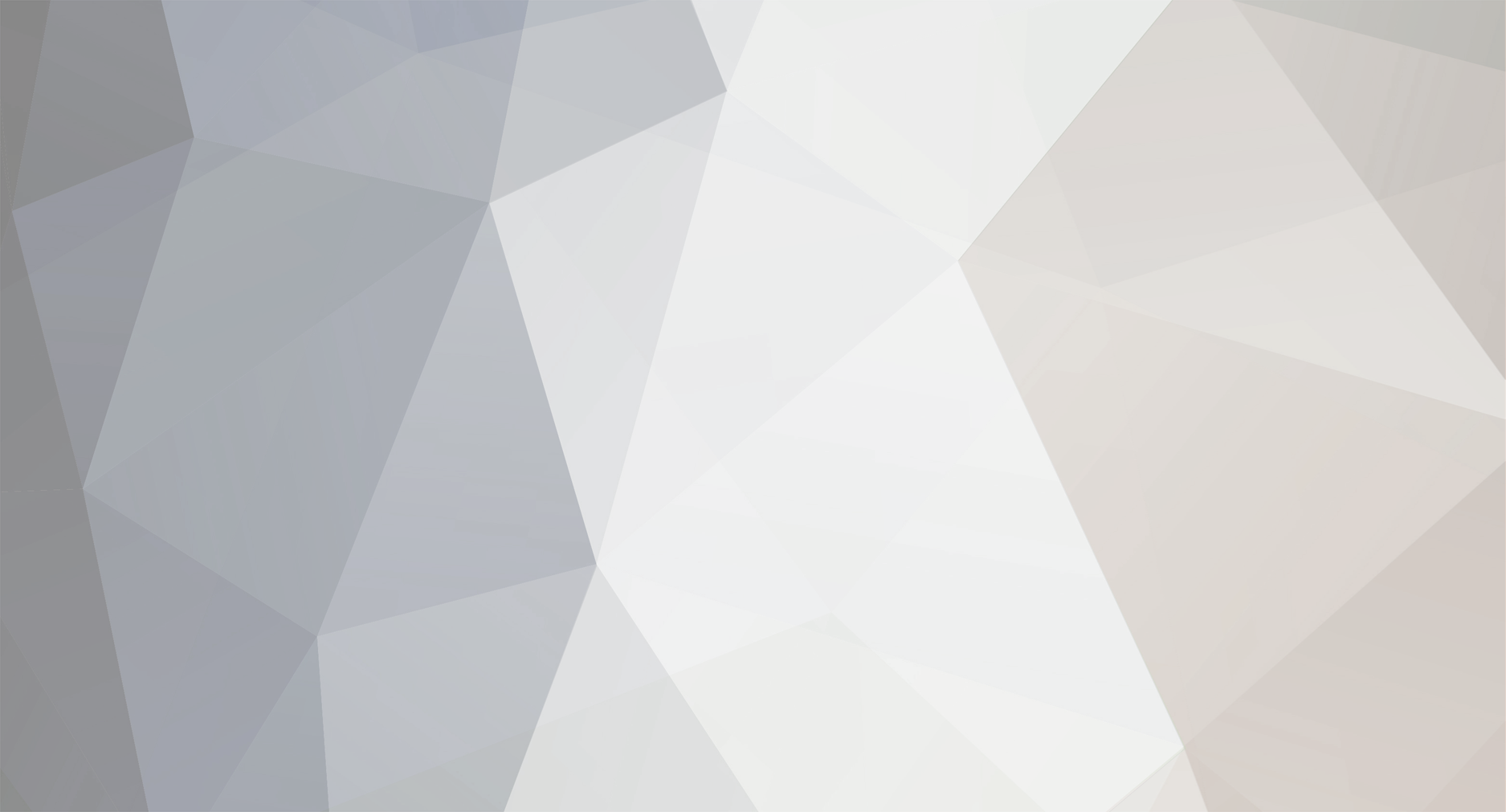
WR1
Administrator-
Posts
985 -
Joined
-
Last visited
-
Days Won
286
Content Type
Profiles
Forums
Events
Everything posted by WR1
-
1. Yes we can allow torsion or anything in a building as long as you are designing for that (uneconomical). 2. Fundamental mode? What is a fundamental mode? A mode with highest mass participation. 3. Why you are just looking at Rz in first mode? From the table you attached, in my opinion; First mode = Mode2 of ETABS with 54.56% mass participation in X direction. (T=0.553s) Second mode = Mode3 of ETABS with 36.33% mp, rotation in Z direction (T=0.505s) Third mode = Mode1 of ETABS with 34.75% mp in Y direction (T=0.586s) Remember that ETABS lists mode based on descending order of T and not mass participation but in my opinion we should sort modes based on mp. Moreover, You have to check that modes are not "CLOSELY SPACED". That means, if you look at T above, you will find that translational modes (T=0.553 & 0.505s) are very close to torsional mode (T=0.586s). This is bad. Try changing configuration of your building. You can still continue designing like that but ofcourse its more economical (bad design). From the data you provided, it looks like your building is undergoing translational+rotational in a complex way all at once. The shape, geometry, configuration of shear walls etc is not regular or you are trying to model a very stiff and very flexible elements together like a concrete basement supporting a light steel roof/canopy.
-
Are you sure its just the change of modifiers that stopped giving errors? I never came across this. Are you sure you are not out-of-plane modifiers to membranes?
-
Please explain, i couldnt understand.
-
I have never found diff between simple moment coefficient method frame examples in etabs. Once everything is okay I can assure you ETABS results wouldnt be much different than manual ones.
-
By what approximations?
-
Yes, beam moments are separate. Strips show moments only for slab areas not for line elements.
-
Ofc SAFE strip forces will be different than those from manual method because of differences in strip widths. What is the strip width in SAFE vs in ACI or whatever method you are using? Also try changing slab from shell to membrane after you have done the above point.
-
You should not reduce it by R if you are performing nonlinear analysis inputting actual R (energy dissipation mechanism). But RSA is a linear method so divide by R (an assumption that building will have ductility in reality so less force).
-
You could use Limcon for steel connections.
-
In ETABS, SAFE, SAP axial forces are F11 and F22 in 1 and 2 directions resp. By default axis, a load applied in elevation to a wall will show axial force as F22. You can sumup/average total axial force by assigning it as a pier width of which depends on the length, spreadout and type of applied load. Axial capacity of wall as mentioned in above reply can be calculated like a column. You can calculate capacities of anything from PMM interaction (atleast for a beam, column and a wall). Just respect the boundary conditions.
- 2 replies
-
- rcc
- axial load
-
(and 2 more)
Tagged with:
-
Well yes contours plots are more (comparatively) realistic than strip reinforcement and economical too. Think of it as you have reinforcement in the form of powder. You put the reinforcement powder (or form like that) on slab based on fea contours. Economical, realistic, interesting and easy. Isnt it? Now unfortunately we dont have powder reinforcement (or atleast i dont know). And we are left with reinforcement bars. For that we need to have some assumptions; width of bar strip width assuming a single bar will cover the contoured reinforcement in a limited width. Complex right. But you have the ability to draw strips in SAFE. But for that you have to decide things like; Strip width Orientation of strips Layers of strips Now that is simple for simple slabs and geometry but complex in your case. But there is no other solution. You gotta decide (based on experience, economy etc) how and at what angle you gonna lay your strips (like actual site conditions). Lets say you find out that 45 degree strips give you more economical reinforcement (probably because fea contours are 45 degrees w.r.t. principal axes of plan). So you on actual site you put the same layout plus any additional reinforcement given by SAFE. So far now we dealt with orientation but what about strip width? Well thats variable practice. According to ACI you can have a very large strip like middle strip averaging all the fea contours in this width. Some people use 1m width (thats very conservative i think, happen a lot in middle east but not in Asia). Because practices worldwide differ due to different economies among other minor factors. For point loads I would not go for a 1m strip. It depend on the location of point load and its spreadout relative to boundary conditions. Check with your industry practice about this. For strip layers, SAFE give you total strip area. Its you who then decide (by changing covers) that how to split total reinforcement in how many layers. Now things really get interesting if you have 12 top and 12 bottoms layers (so cover is huge factor now) with some layers orientation different than others plus extent of some layers is also variable. And I know how crazy this is to handle with SAFE. But if you do have a better reinforcement software you could use that. So it all depend on your interprettation. For the high values of concentrated reinforcement it all depend on how would you average out the contours. Is the concentration due to point load? Is it due to a corner, mesh, singularity in FEA solution?
-
Well saying things n implementing them are 2 diff things. This note is for myself n not trying to shatter ur beliefs. Because its very difficult. Unless u have lot of money u cant do that. And business in pak is all abt survival. Think abt developed and poor countries and their welfare for people. My idea is less working hours max 6 hrs a day. 2 days off. Weekday holidays. A good salary package ideally the share holder in company shares. Working on big picture not the small things. Small but important facilities like chairs kitchen proper seating, friendly env, no crazy n complex bullshit like waiting for approval of leaves on companies online system. Do it on the spot. Right away on the spot. A sense of responsibility and achievement and satisfaction. A work life balance and equal growth opp for everyvody. Its not that iv been a victim of all above, its just that iv observed all this in firms. Personally id been quite well n comfortable in companies iv worked but theres a lot more to do.
- 13 replies
-
- structural firms
- structural firms pakistan
- (and 2 more)
-
Yes 25% is for warehouse, Usually only 100%D is enough for normal buildings, but you need to consider all the Live Loads and Dead Loads that are permanent. For example if you have permanent mechanical equipment as Live Load then consider then in mass source too. If a portion of live load is assumed to be sustained for example where LL is heavy like in malls, a portion (~25%) of LL should also be considered. In summary, any load that is deemed to be permanent...consider that in seismic weight calculations.
-
Instead of uniform thickness, may be you can provide variable thicknesses? For example, the raft slab at right and left areas can be reduced. You can provide more thickness in middle area where there are columns and walls. Similarly you can provide a more thick continuous strip footing all along the parameters under the perimeter columns. Then you can add local thickening directly under the edge/corner columns too. Tie the edge columns with stiff beams at a level above raft (at gf for example) to connect them together and make the whole thing as one unit. At the end satisfying bearing pressure for this kind of foundation is very difficult at the perimeter, so at any cost you gotta connect them by stiff strip (preferably straps/beams) foundations.
-
I heard about Bilal & Mushtaq in Karachi. They do lot of highrises. In the end and based on my exp, work never ends in any firm. experiences vary. But its all routine, its all typical. Self study and hard work is everywhere. But I am more interested in "work culture" and employees care. All firms are doing business, earning money, and you work for them. I have never seen/heard about a good company in Pakistan or abroad that has a nice relaxed work culture and relations for structural engineer :p. So good luck for choosing structural engineering practice. An no one to blame, even if you open your own consulting firm, you would follow the same old boring routine...it all depends on money coming in.
- 13 replies
-
- structural firms
- structural firms pakistan
- (and 2 more)
-
Stiffener Modifiers for Shear wall in STAAD Pro
WR1 replied to Ahmed Waqar's topic in Software Issues
Yes you are correct as Umar said but you results might not match with ETABS as you would be reducing everything by E (A for shear and axial, I for bending). Generally reduction in GA is not done. But it all depends on what type of stiffness is dominant. Or these squat walls where shear stiffness governs or tall walls where flexural deformation govern? If flexural deformation, you could change E and the effect from shear would be minor. But remember that axial and bending stiffness in a wall are inter-dependent (regardless of the software). Changing one affects another. There might be many possibilities. 1. Change E (affects EI, EA and GA as G depend on E unless you put different or original G). 2. Change thickness (affects EI, EA and GA). This is the case of ETABS modifier. m modifiers internally affects t³ and f modifiers internally affects t. But if you change t outside in material properties like in STAAD, you would affect all the m and f modifiers. So from the above discussion, I would go for option 1. Change the E (only for walls), but dont calculate G based on new value of E. It depends if you want to reduce shear stiffness too or not. Another point now is that what value you would choose for E? Is E=0.7Eold... The easy answer is use your judgement (:p). Another way is to compare results with ETABS, but would you make another model in ETABS? Because comparing with simple example might not be efficient in this case. At the end you need relative stiffness of other members too. To go a little deeper; A) Axial stiffness of wall = in-plane bending stiffness of wall = Eh/(1-v²) f modifiers in ETABS affect this h. (f11,f22,f12). You can change E here as well (but make sure to check the value of G as it is affected by E in some programs like ETABS). But in ETABS there are 3 modifiers, in STAAD if you change E or h, it would change all f11, f22, f12. So you have to make sure is it flexural dominant wall (f22)? a spandrel (f11?) or shear dominant wall (f12?). Other wise h or E in staad will affect all f. B ) Out of plane stiffness of wall = Eh³ / 12 (1-v²) So in ETABS m modifiers affect this h³. Meaning 0.7m is equal to 0.7 (h³). Again here, reducing E or h directly reduces everything (m11, m22, m12). Its like you just using a new all with reduced h and all properties are based on this new h. At the end, see what case you have? #1 Are you designing the wall as in-plane (shear wall) or out-of-plane (basement wall)? #2 Which stiffness is controlling? x. Shear y. flexure z. shear+flexure? Lets assume its an in-plane shear wall. For x: Change G only For y: Change E only For z: Change G and E both This is purely my own understanding. Others are welcome to suggest. -
Strap beam can be designed a normal beam taking negative moment at mid span. They are generally not designed to take soil reaction and are separated by a flexible layer from soil. You can read for example in Nilson book about the design guidelines.
- 6 replies
-
- footing design
- foundation design
-
(and 2 more)
Tagged with:
-
Stiffener Modifiers for Shear wall in STAAD Pro
WR1 replied to Ahmed Waqar's topic in Software Issues
I think in most of the programs G is automatically calculated based on E and v but double check. And it is not always good idea to change E instead of I for stiffness reduction. Because E can change EA, EI and GA as well. -
For the last point, I would like to add that stress would go on higher and higher if you keep refining your mesh due to introduction of singularities in the solution at corners and under point load. So at what level you would stop doing the refinement. Yes the sensitivity analysis is performed to compare mesh refinements but for this particular case what would be the basis? deflection under point load?
-
If there is a concentrated point load in the middle of a two way slab. What is the best way to take out realistic results. Also what would be the best judgment to calculate strip width. As you know, the size of the stress contour and its magnitude depend on the mesh size too. So what would be the realistic value to use.
-
What could be the purpose of reducing raft stiffness by 60% (m11=m22=m12 modifiers of 0.4) in SAFE Model?
-
Default Skin
WR1 replied to UmarMakhzumi's topic in Website Announcements/ Problems/ Login/ Registration Issues
Idk but the new skin I'm seeing is pure love. -
It is something to do with your storage drive as you said, if you move it to another location it works fine. Also check security/scan settings for the drive in which you are working. Is it interfering/accessing the same files as ETABS does? Not exactly this but I have come across "failed to retrieve joint" errors sometimes when I run directly in our office servers. So I save it on my local pc and run and then save back to the servers.